Silicone Injection Molding
- 22 Injection Molding Machines
- 4,000 m2 Injection Molding Workshop
- Germany & Japan Brands
Liquid Silicone Injection Molding
Liquid silicone rubber injection molding is also referred to as LSR injection molding, it is a robust process for high volume silicone production. Miwo has excellent experience and capability to produce LSR components with varied geometry. We are able to handle low viscosity of LSR and avoid flashing tendency. Our high quality liquid silicone injection molding has unique characteristics:
- Flash-less molding
- Complex part geometry
- Fast curing cycles
Silicone Injection Molding Materials
The silicone material in injection molding process is liquid silicone rubber (LSR). This liquid silicone material is supplied in a two-part drum. In this two component system, Part A contains the vinyl functional polymer, while Part B consists of the cross-linker and inhibitor. The low viscosity LSR materials is pumped into the injection unit of LSR injection molding machine or LIM molding machine.
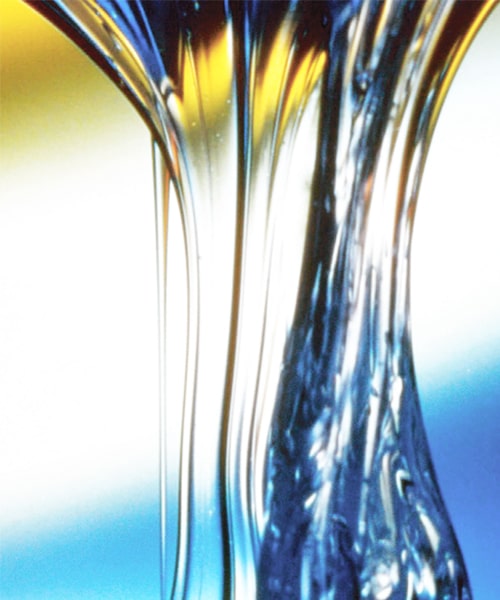
Liquid Silicone Injection Molding
The silicone material in injection molding process is liquid silicone rubber (LSR). This liquid silicone material is supplied in a two-part drum. In this two component system, Part A contains the vinyl functional polymer, while Part B consists of the cross-linker and inhibitor. The low viscosity LSR materials is pumped into the injection unit of LSR injection molding machine or LIM molding machine.
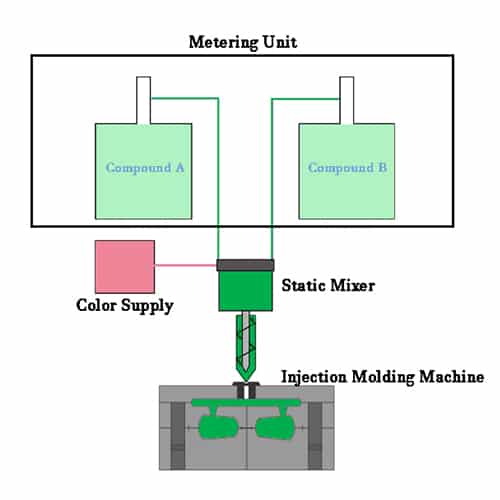
LSR Characteristics
Liquid Silicone Rubber has natural manufacturability, LSR molding provides advantages of easy processing, high-volume molding, consistent quality and high productivity.
LSR is the ideal material for the critical demanding applications in reason of its unique properties:
- Bio-compatibility: Liquid silicone rubber (LSR) is superior compatible with human tissue and body fluids in extensive tests. Comparing to other elastomers, liquid silicone rubber is resistant to bacteria, and never corrode other materials. LSR can be formulated with stringent FDA requirements. It also can be sterilized by different methods, like steam autoclave, ethylene oxide, gamma, e-beam.
- Durability: LSR is able to withstand high temperature, this make it perfect for components with high temperature resistance demands. In addition, LSR parts are fire retardant without melting, this makes it better performance than plastics.
- Chemical Resistance: Liquid silicone (LSR) can resist water, oxidation and other chemical solutions like acids and alkali.
- Temperature Resistance: The liquid silicone rubber can withstand wider range of extreme temperature than elastomers. Such as Dow Corning LSR is stable in temperature range from -60℃ to+180℃.
- Mechanical Properties: LSR has excellent elongation, high tear and tensile strength, good flexibility. Its hardness range from 5 to 80 Shore A.
- Electrical Properties: Liquid silicone rubber has excellent insulation properties, it is an appealing option for electrical applications. LSR has wider performance temperature than conventional insulating materials.
- Transparency & Odorless: Liquid silicone is natural transparent and odorless, it can be molded into colorful and custom parts.
Liquid Injection Molding
LSR Design
Liquid silicone rubber molding is adhering to fundamental design rules of injection molding, while we can produce stronger components with easier fabrication and assembly.
- LSR molding is a complex process with functional and structural requirements, this LSR molding design should include: intended usage, assembly fitness, experienced loads of LSR parts.
- Molded features of LSR parts should depend on how LSR materials inject, fill and cool down in molds.
- Setting appropriate tolerance and additional features in design to minimize internal stress and reduce flash.
LSR molding can fill the thin wall section with minimal challenges, it can accommodate wall section variations without virtual sink issue.
LSR Tooling
All precision LSR parts start from the precision LSR tooling, these molds are produced by combinations of CNC machining and EDM. It will take a great amount of time and accuracy to high-temperature LSR molds, in order to hold up the LSR molding process. All LSR molds should take challenges as following:
- High precision (LSR viscosity)
- High temperature (nearly 200℃)
- Wear resistance(LSR abrasiveness)
LSR tooling is the longest step with the largest investment in LSR molding process. Otherwise, LSR natural properties make it able to flow into thin cross-sections, tight radii, thick and thin features, this will reduce the mold design difficulty. Normally, LSR mold surfaces don’t require highly polishing surface, draft angles are not necessary for finished parts removal. Once LSR materials are solidification in molds, never need to concern distortion or damage in ejection process.
LSR Injection Molding Benefits
Miwo apply liquid silicone rubber to produce precision silicone parts and over-molded assemblies with near flashless. Our high quality silicone parts have high reputation in global customers. Liquid silicone rubber has wide application in reason of its key advantages:
- High-volume production: LSR injection molding is perfect for cost-effective and high volume silicone production with complex structure.
- Low contamination rate: LSR manufacture process is in a closed system, this reduces the contamination possibility.
- High automation level: LSR injection molding is equipped with automation of injection, tooling and ejection, this give rise to minimal labor cost to monitor system.
- Quick cycle time: LSR molding production has short cycle time, otherwise, this cycle time will be determined by following elements.
Custom Silicone Injection Molding
Miwo has concentrated on silicone molding for 20 years, we are the most experienced manufacturer of LSR injection molding technologies. Our expertise encourage us to tailor the entire process for your specific demands, take your custom innovation into a new level.
We are the leading silicone parts manufacturer in China, we are able to serve all enterprise and companies in worldwide. Our advanced capability can encompass every aspect from design to production. We can assist you to select the perfect LSR grade, optimize design manufacturability (DFM), provide premium-quality tooling, high-volume production and packing solutions. Our high-quality LSR parts are widely applied in automotive, medical,
Contact us now for your new silicone injection molding project.