Liquid Silicone Rubber (LSR) is a two-part catalysis-cured thermoset elastomer, we normally inject LSR materials into mold cavities to produce final silicone parts. This material provides properties not obtainable with TPE. Therefore, LSR is very versatile in elastomer industry, it is widely applied in various industries from consumer parts to medical devices.
The normal operating temperature range of LSR is between -65℃ to 150℃, shortly peaks to 260℃. After solidify formation, LSR has very low compression set. These thermoset polymers are translucent, and can be pigmented to match any color requirement. In addition, LSR has shorter cycle time and less raw material, this result in quicker delivery time and higher production.
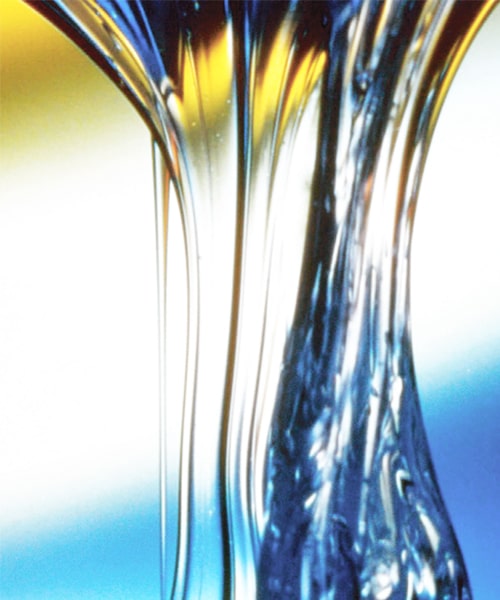
LSR Polymer Manufacturing
Like all elastomeric materials, liquid silicone rubber requires a polymerization reaction to create molecular chains. Such as vinyl and methyl siloxane are polymerized into polydimethysiloxane chains. These molecular chains can provide strength and flexibility to LSR material. This process will transform LSR from liquid of water starting compounds into basic viscous material.
We also can design additional properties into this material by polymer chains enforcing. After creating the original polymer, we will add fumed silica into this material to reinforce. Different from fill plastic organic materials with carbon black or pigmented clay. LSR material normally use other silicates to reinforce polymer chains and increase tensile strength.
Then, we will split the polymer material into two hales, add the catalyst and cross-linker separately in different halves. This will increase the shelf life of these two materials (Normally LSR/A and LSR/B). In splitting these halves, these materials can be stored for year without worry about curing formation. However, once these two halves blend together, there is short working time of eight hours in average.
Liquid Silicone Rubber Types
There are different types of Liquid Silicone Rubber materials. Normally, we divide these LSR materials by different industrial applications.
Medical Grades LSR
Medical LSR materials have very strict requirement to avoid interaction with tissues. It is a challenge to select an acceptable silicone for medical applications, the most critical issue is to determine the biological response of LSR material or formulation to direct or indirect patient contact.
Medical grade LSR has different curing system comparing to conventional silicone. However, the best curing system for medical silicone is platinum cure system, it apply vinyl-functional polymers, oligomers with Si-H groups, and a metal complex catalyst (like organ-metallic complex of Platinum salt). This curing system has no by-products. Then post baking press will assure fully cross-linking in silicone parts. Otherwise, there may be effects on compression set and out gassing.
Liquid silicone rubber formulations for medical applications are in accord with specific evaluation standard of ISO10993, which evaluates the material biosafety in contact with human body. According to this standard, LSR silicone is divided into three categories:
- Limited exposure LSR: Limited exposure LSR products have up to 24 hours service life in contact with skin, breached surfaces, or mucosal membranes.
- Prolonged exposure LSR: Prolonged exposure LSR products are also health care grade, which have contact with surface or are implanted more 24 hours and up to 30 days.
- Permanent contact LSR: Permanent or long-time contact LSR products are able to implant for more than 30 days.
The testing methods and results of medical grade silicone must be accessible for customers, and validated by FDA. Meanwhile, the test of silicone grades are on base of cyto-toxicity, infra-cutaneous reactivity, sensitization, toxicity, histopathology, haemolysis, cancernogenicity or others.
Self-lubricating LSR
Incompatible fluids compounds mix into this LSR material, after silicone curing process, this material will create a slippery surface by material blooming. Normally, we can add 1.5 to 3 percentage of phenyl fluid silicone, this depends on the fluid blooming rate requirement of customers.
Conductive LSR
Medical grade liquid silicone rubber is an excellent material, it has high stability in a wide range of temperature. In the extreme temperature from -65℃ to 250℃, this LSR materials can retain its properties of resiliency, flexibility, and mechanical force transmitting ability.
Self-bonding LSR
We also can add adhesion promoters into LSR material, in order to provide primerless adhesion to different substrates. This grade LSR can work well with stainless steel, glass filled nylons, aluminum and plysulfones. Therefore, this LSR type is the perfect solution to reduce assembly components for composite seals, and provide better sealing in tow mating components.
FLSR (Fluorosilicone LSR)
Medical LSR parts with injection molding process will create products with excellent surfaces, all these surfaces are dry feeling and non-tacky to touch. In addition, we also can achieve different texture by customizing surface in mold cavity in liquid silicone molding technology.
Radio Opaque LSR
We normally add barium sulfate into LSR to create Radio Opaque LSR, it is detectable under X-ray. Therefore, this material is suitable for medical applications like wound drains and catheters.
Flame Retardant LSR
Most LSR rubber can satisfy UL 94 H-B classification flammability requirement without any additives. For higher classifications, such as UL 94 V-1 or UL 94 V-0, additives with water relesing once decomposed in LSR will achieve these standards.
Fast Cure LSR
Functional groups can combine with LSR material to determine the cross-linking level of the elastomer. We can control these functional group levels to determine final cure sites reactions in materials. This will result in high reactivity of LSR, and quick production cycle times for mass LSR parts production.
LSR Molding Process
Once we select High consistency rubber(HCR) materials to produce silicone parts, we need to transform raw silicone materials into mold-able size and shape for mold cavities. This process is performing silicone material. Some silicone materials also need an extra step to add cures.
However, LSR manufacturing process will remove all of those steps. We summarize LSR molding process as the following:
- LSR A/B compounds are typically in 5 gallon pail or 55 gallon drum. The pumping kit will press on the buckets, and force these materials into a static mixer and feed into the injection unit.
- Then we can also add pigment into mixed compounds with controlled stream. In the injection process, materials will be mixed with additional screws and pushed forward into material shots, in order to fill the mold cavities.
- After LSR materials are injected into molds, the molds will stay clamped together and cure LSR materials. Then operators or robots will remove cured silicone parts from the mold and repeat this cycle. This is a quick, efficient process, the normal cycle time of LSR injection molding is 30 seconds.
- Secondary operations, like post baking, can reduce volatility and improve compression set. Or de-flashing, will remove unnecessary flash. Then clean and remove foreign materials for packaging.
Comparing with organic materials or high consistency silicone, LSR has a significant cost savings in labor cost over HCR. The average cycle time of HCR molding is around 6 minutes, while peroxide cured materials will take even longer to 9 minutes.
Benefits of Liquid Silicone Rubber
LSR has high electrical stress resistance without impact on final product conductivity. It is the most common material in high-voltage application and electrical parts.
- Superior heat stability: Liquid silicone rubber can withstand high temperature up to 200℃ without melting or creeping. This make it a perfect option for seals and gaskets in heavy-duty and automotive applications.
- Low-temperature flexibility: Thermoplastic elastomer (TPE) will lose flexibility at extreme low temperature, it becomes hard, brittle and crack. However, LSR is flexible at temperature at -40℃, it is an excellent material choice for products in low-temperature environment.
- Chemical resistance: LSR has excellent chemicals’ resistance in extreme temperatures, while TPE can only provide chemical resistance in moderate temperature ranges.
- Low compression set: LSR low compression set can resist permanent deformation in constant strain, LSR has a very low compression set in range of 15%-20%. Even in extended periods of time and different temperature ranges, LSR also can retain its elasticity.
- Aging resistance: Cured LSR has excellent resistance to UV rays, weathering and aging. It is idea for applications with long-term exposure environment.
- Shelf life reliability: Most LSR products has shelf life of at least 1 year, it is a key factor in fabrication environment.
- Electrical resistance: LSR has high electrical stress resistance without impact on final product conductivity. It is the most common material in high-voltage application and electrical parts.
If you are interested in our liquid silicone rubber materials and fabrication, contact Miwo engineering team now.